At the 2018 Bay Area Maker Faire, our project Uncovering the Silicon showed off a number of simple and complex integrated circuits (with rather large feature size) under the microscope. We had a great time helping visitors look at the features and get a glimpse of what’s inside those black box integrated circuit packages. To take this to the next level for this year’s Maker Faire, we decided to try and close the loop; to take one simple integrated circuit and elucidate its workings well enough that visitors to our booth will be able to see every single component of the circuit, understand their function, and relate it to the macroscopic behavior of the chip. For this, we picked what turns out to be a rather obscure chip: the Fairchild μL914, which is a dual 2-input NOR gate. This chip belongs to the resistor–transistor logic (RTL) family.
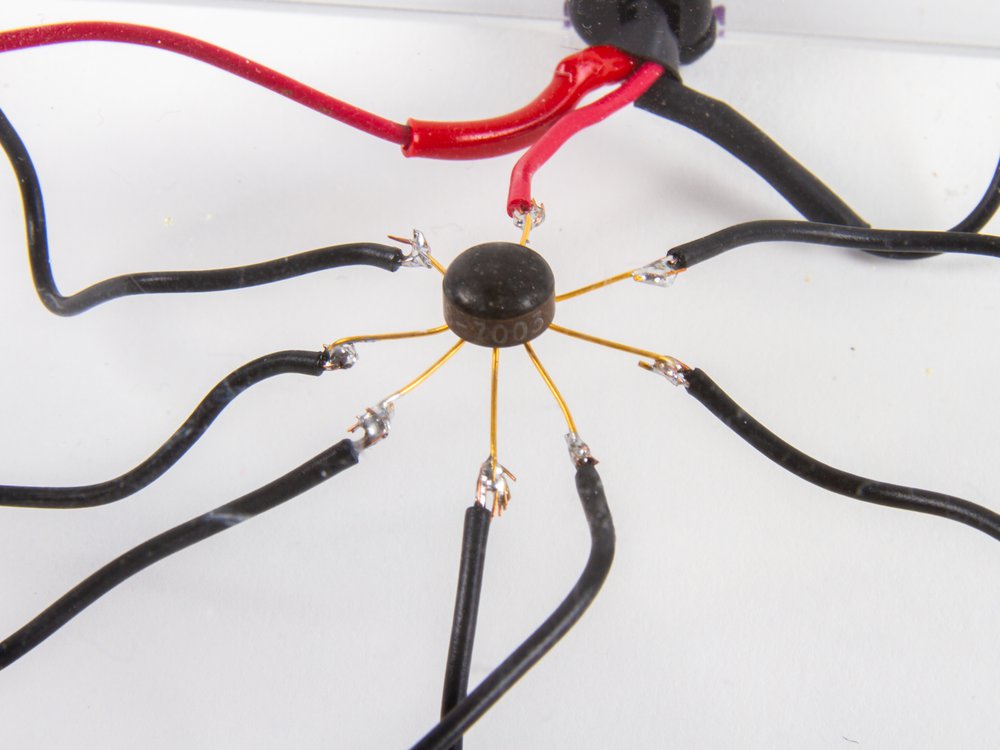
Here’s what the chip looks like. It’s in a funny old “glob-top” can package with eight leads.
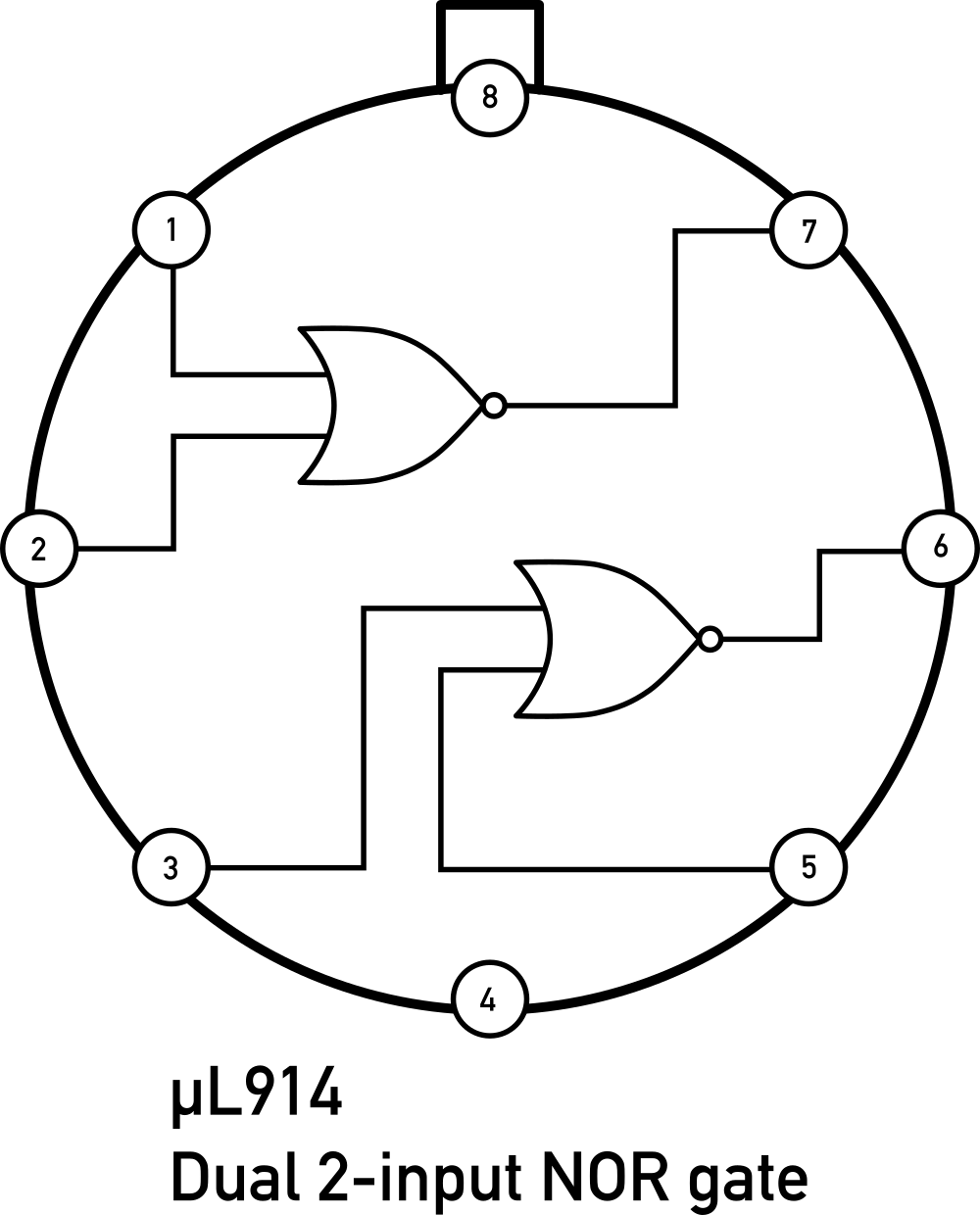
Here’s the pinout; there are two NOR gates in the chip, plus power and ground.
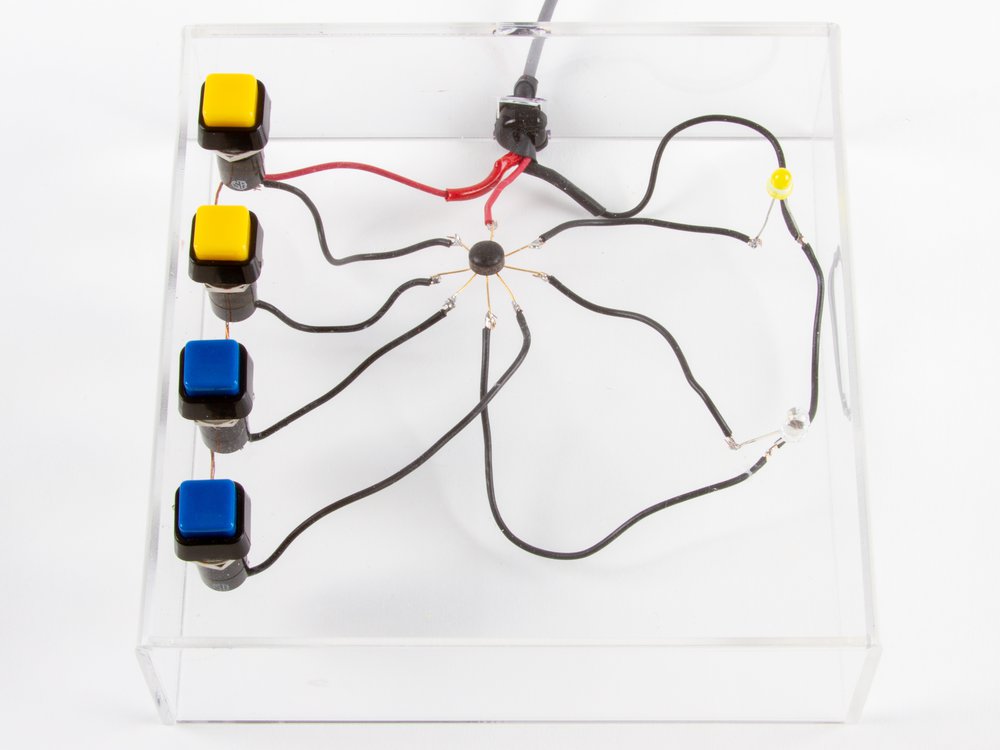
Ken Shirriff built a circuit with the chip to demonstrate its functionality. When we push either of the two buttons for one of the gates, that LED will turn off.
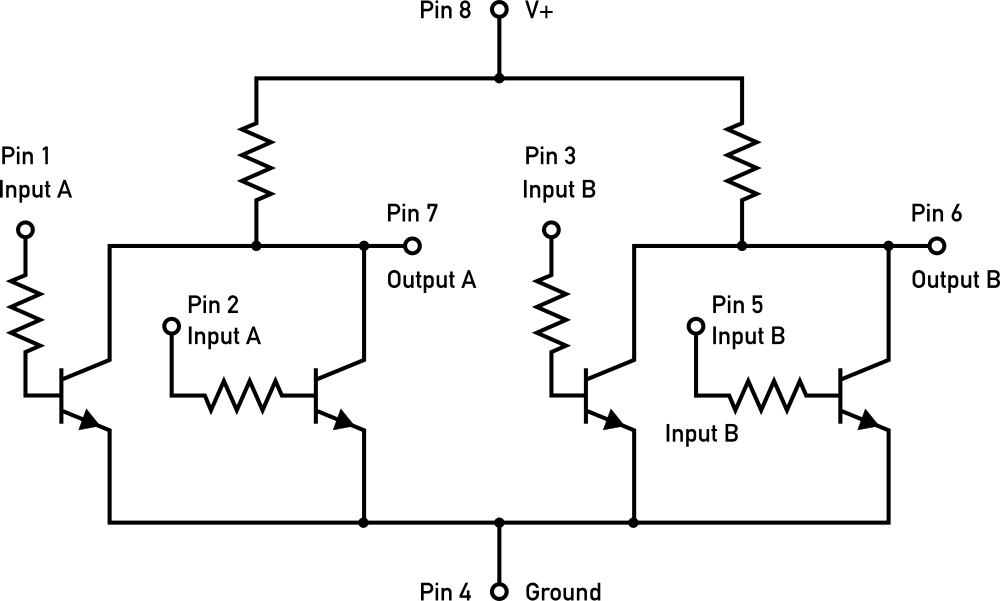
Here’s the schematic diagram, adapted from the original datasheet. If you look at the left side, if either of those inputs goes high, the transistor pulls the output low.

John McMaster decapped a few of the chips and sent us a die photo. He made a video about the process — no small feat. We’ll be bringing one of these bare chips and a microscope (equipped with both eyepieces and a camera) to Maker Faire.
For the macroscopic scale, we approached visualizing this circuit from a couple of angles: the physical structure of the chip, and the electronic structure of the circuit.
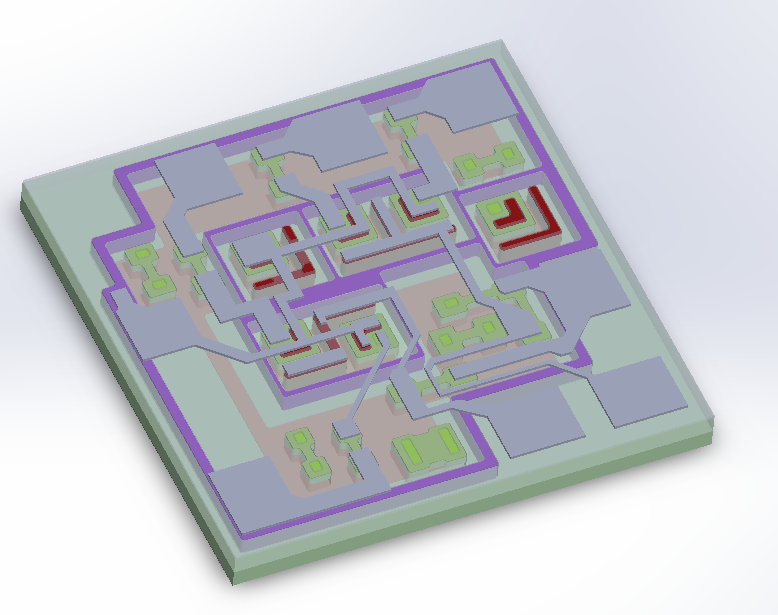
Eric Schlaepfer used the die photo to model the structure of the chip in CAD.
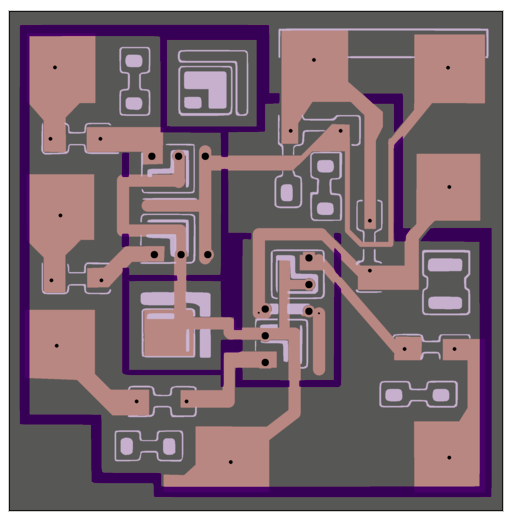
Simultaneously, Ken designed a printed circuit board version for use with discrete components that maintained the same structure as the IC.
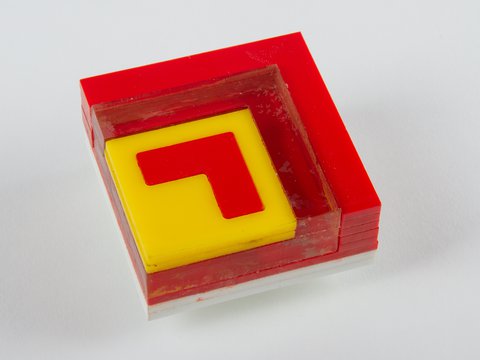
Working from Eric’s CAD model, we built a single NPN transistor model from layers of colored acrylic. If you lift it up, and look through the transparent middle layers, you can tell that the emitter (red) is embedded into the top of the base (yellow) and does not go all the down way through it. (Transistors like these are planar: The emitter is above the base, and the base is above the collector.)
The top layer of this little model has labels for the collector, emitter and base. It is removable so that the layers of the model can be more easily inspected.
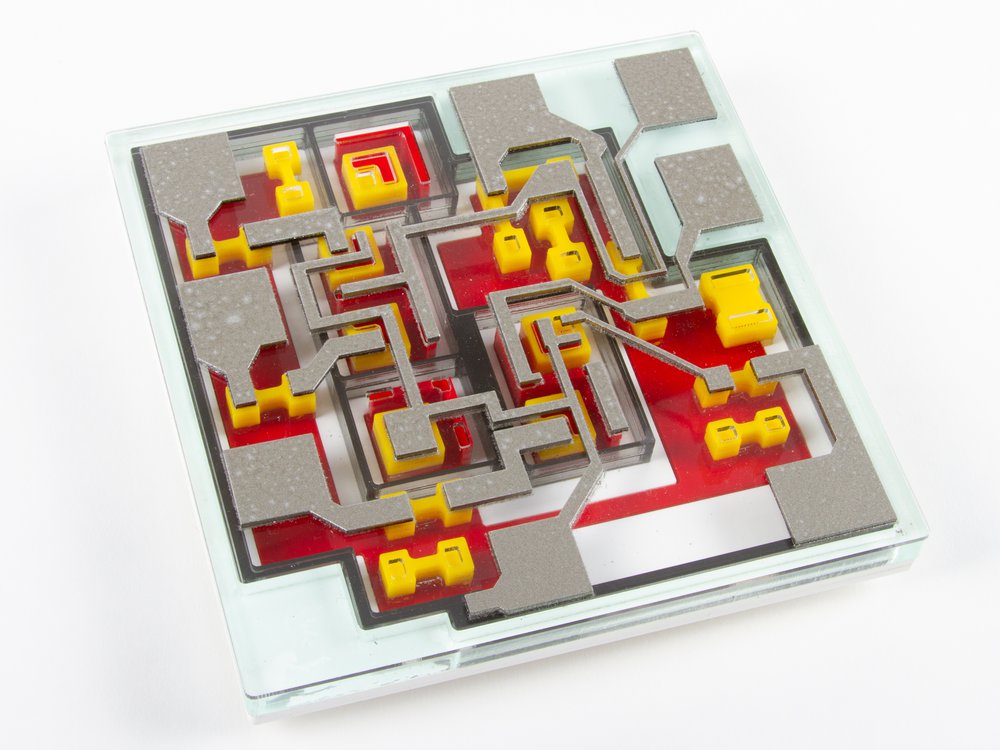
The model of the chip die includes a transparent cover representing the oxide layer, and that supports the metal layer with the wire bond pads on the edges.
One of the reasons that this particular chip is educational to look at is that there are a few unused components on the die. There are two unused transistors: one of them is unconnected, and the other is shorted. There are also several unused resistors (resistors are the dogbone shapes). The unconnected and unused components are easier to see, and provide a visual example that is useful for understanding what the connected components look like under the metal layer.
It is also fun to imagine what other circuits could have been made with different connections.
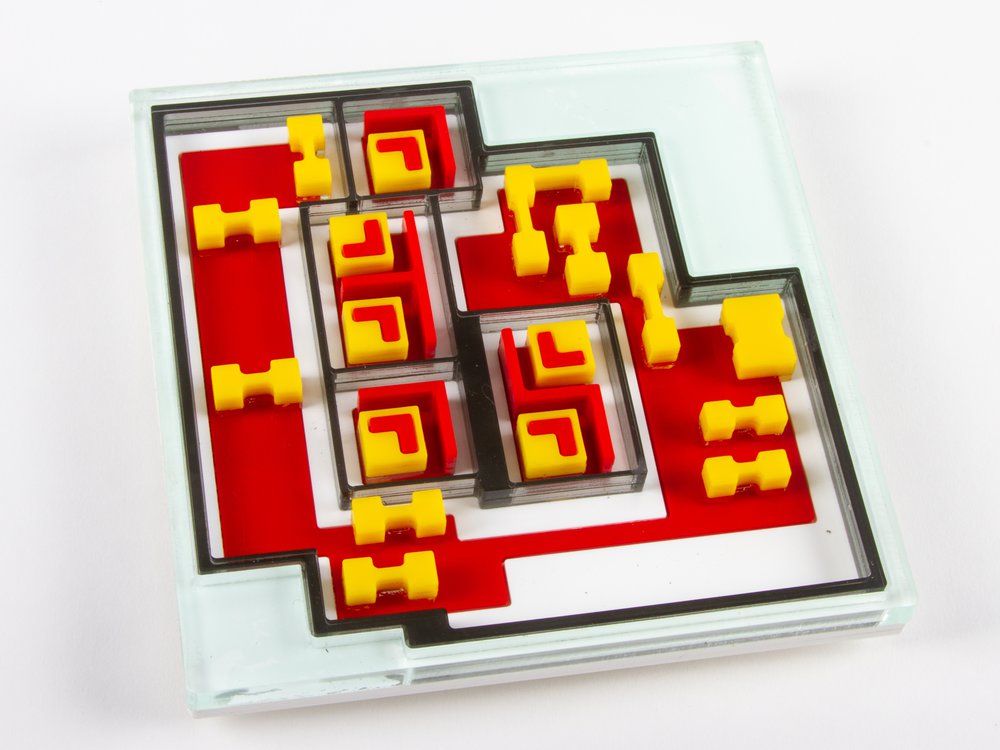
We glued most of the layers together, but left the top two layers removable so that it is easier to see the internal structure when the top is removed.
(Aside: we left out most of the epitaxial pocket material, because even though we used transparent acrylic to represent it, the layers of the components are much more visible without it present.)
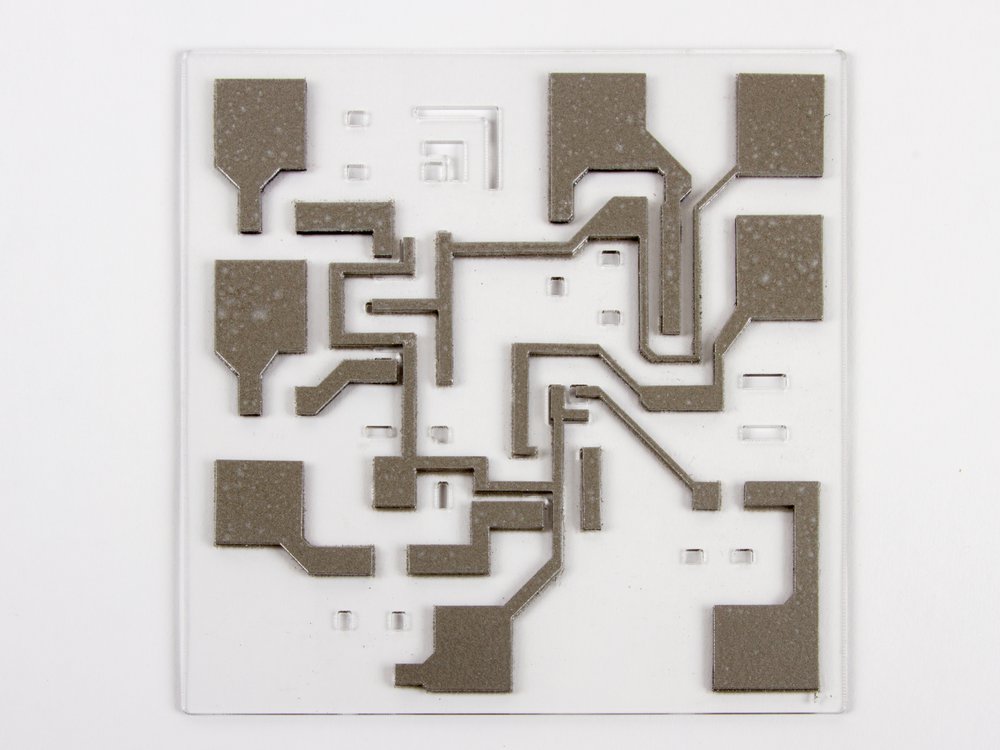
There are cutouts in the oxide layer where the metal layer connects to the circuitry below.
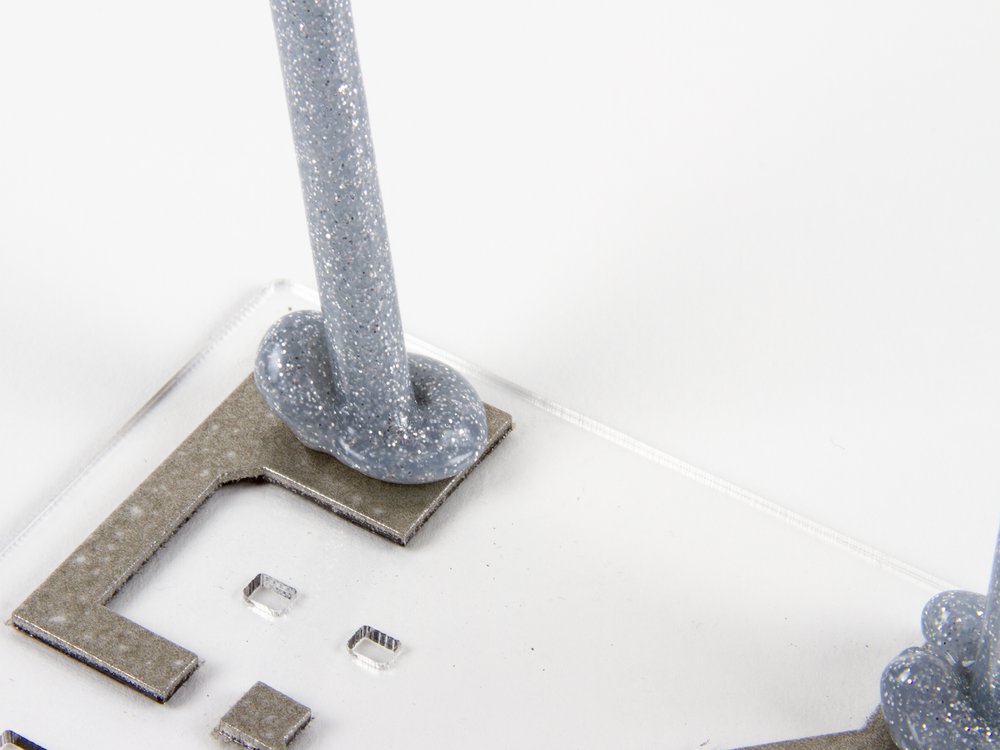
One of the most noticeable things you see when you look at this type of IC under the microscope is the bond wires. We’ve used silver glitter hot glue sticks to represent them.
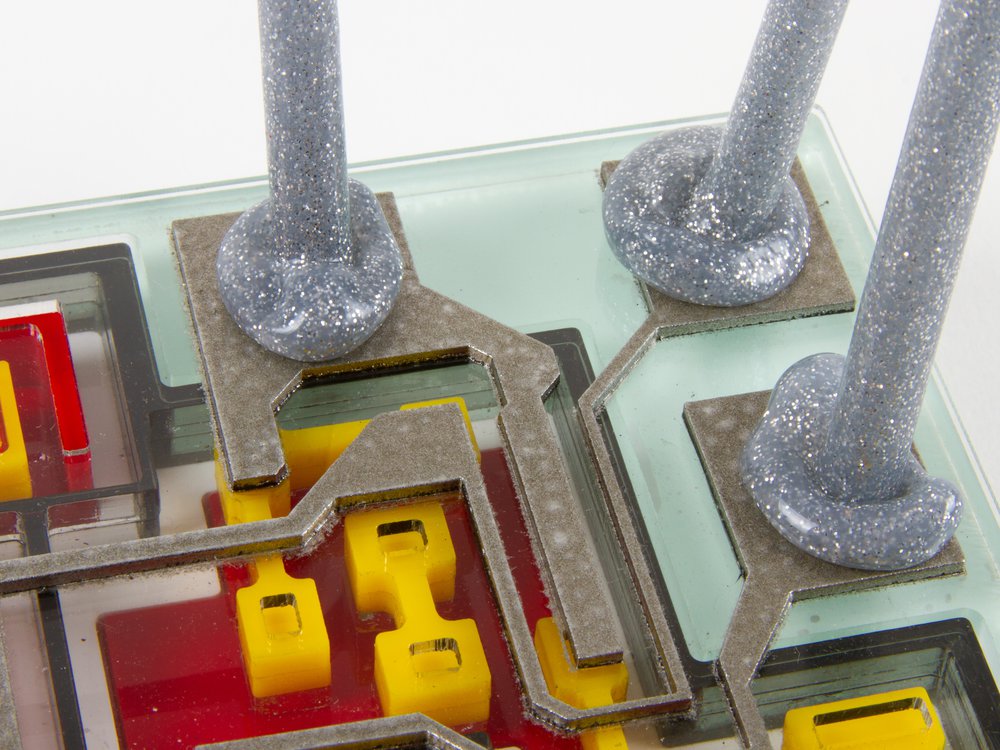
The glob of melted glue represents where the wire is bonded to the pad.
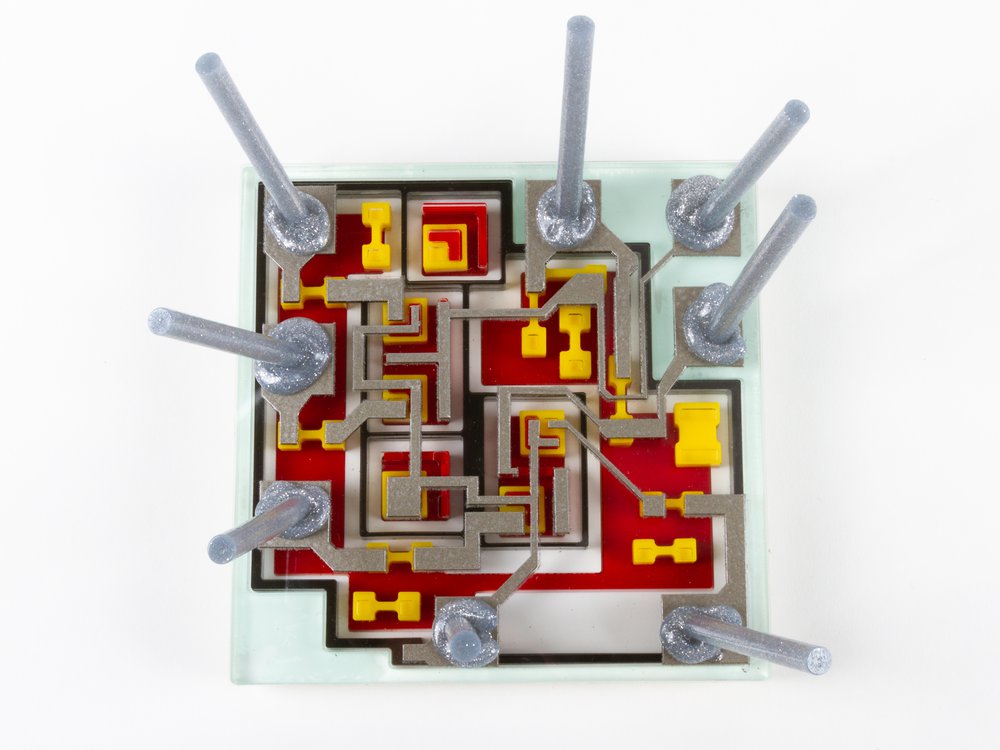
When you look straight down on the model with its glitter bond wires, it looks very similar to what you’ll see in the microscope.
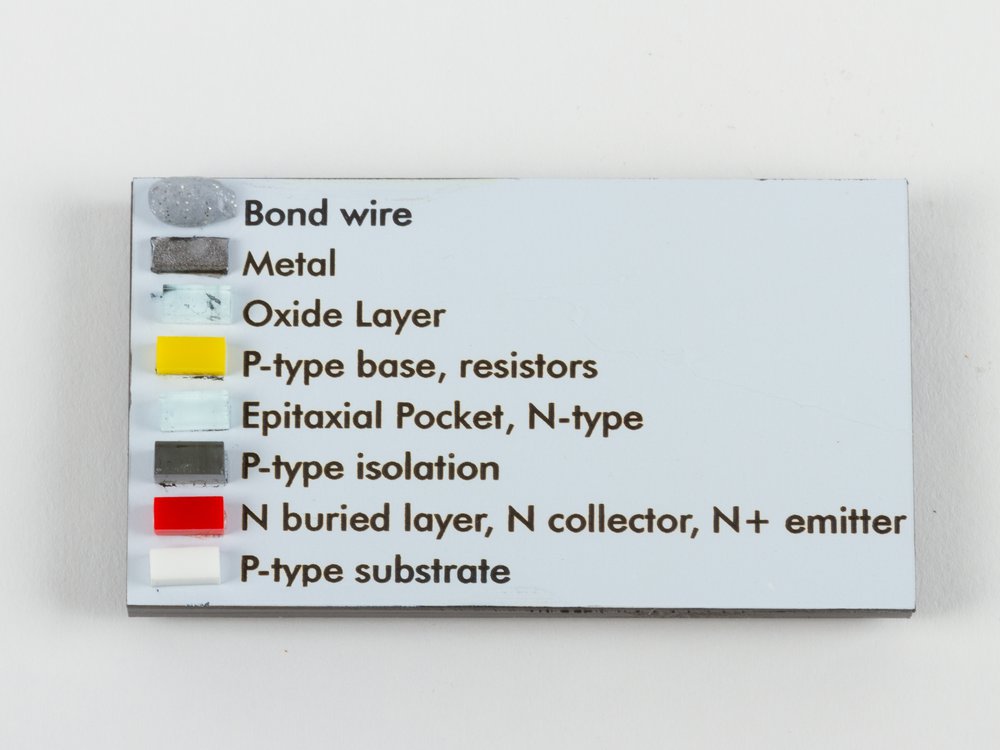
To round things out for our acrylic model, we made a physical legend to make it easier to identify all of the parts of the model.
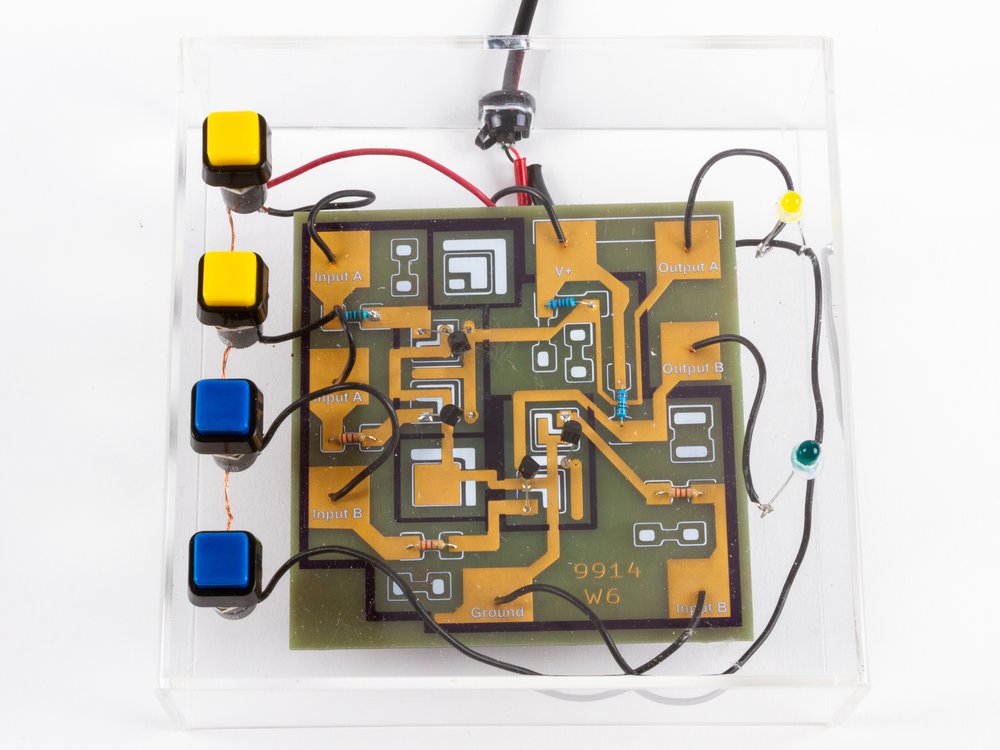
Once Ken got his PCBs back from our friends at OSHPark, he built it up with the same example circuit.
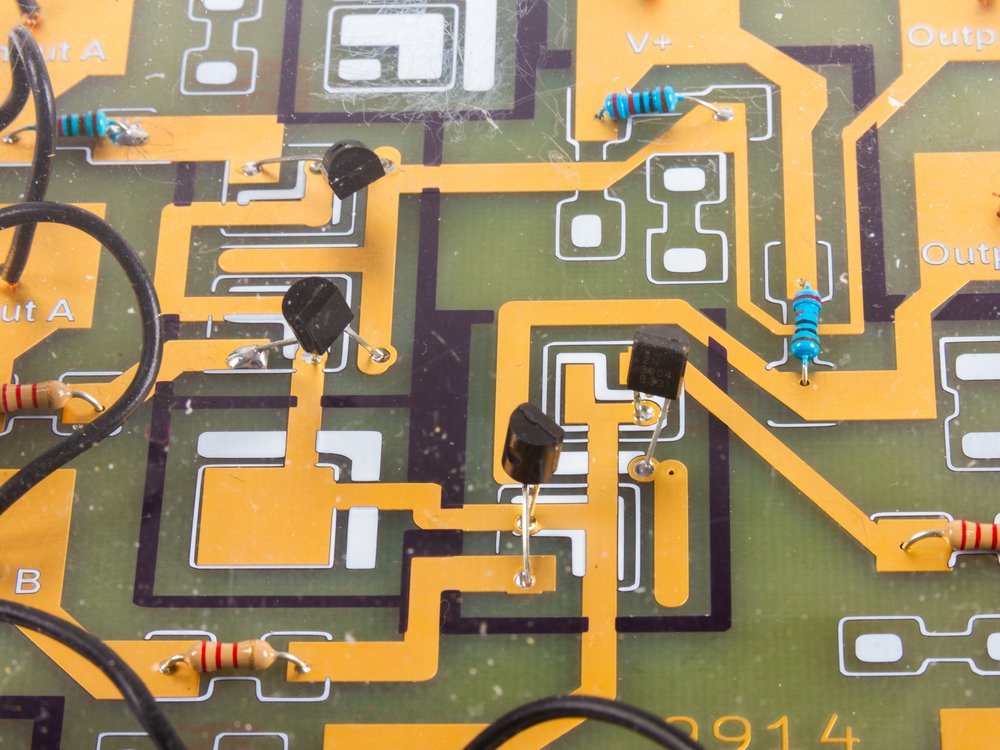
The PCBs turned out beautifully, and it’s great to see the familiar discrete packages on the enlarged circuit. Ken has published the PCB design on Github.
We hope to see you at Maker Faire this weekend!
Bonus: Ken laid out some hypothetical alternate metal layers to use the same die to create different chips.
Bonus video: Mike from Hackaday came to visit our project at Maker Faire and got a great video explanation of our project with Windell. He also wrote it up for Hackaday.